In the ever-evolving landscape of construction methods, prefabricated construction, or “prefab,” has emerged as a viable alternative to traditional on-site building processes. Prefabrication involves assembling components of a structure off-site and then transporting them to the construction site for final assembly. This article aims to explore the pros and cons of prefabricated construction, shedding light on the advantages and challenges associated with this innovative building approach.
Pros of Prefabricated Construction:
- Speed and Efficiency:One of the primary advantages of prefabricated construction is its efficiency in terms of time. Prefabricated components, often manufactured in controlled factory environments, can be produced simultaneously with on-site preparations. This parallel processing significantly reduces construction timelines, making prefabrication an attractive option for projects with tight schedules.
- Cost Savings:Prefabricated construction can lead to cost savings in various ways. The controlled environment of a factory allows for better management of resources, reduced waste, and optimized labor efficiency. Additionally, the faster construction timelines contribute to lower labor costs and potentially lower financing expenses.
- Quality Control:Manufacturing components in a controlled factory environment enhances quality control. Strict adherence to design specifications, precision in fabrication, and standardized processes contribute to higher overall construction quality. This can result in buildings that meet or exceed industry standards in terms of durability and structural integrity.
- Reduced Environmental Impact:Prefabricated construction often generates less waste compared to traditional construction methods. The controlled production process allows for better material optimization, and excess materials can be recycled or reused. Additionally, the streamlined on-site assembly minimizes disturbance to the surrounding environment, making prefabrication a more environmentally friendly option.
- Design Flexibility:Contrary to the misconception that prefabrication limits design options, modern technology allows for a high degree of design flexibility in prefab construction. Customization of components in the factory allows architects and builders to create unique and aesthetically pleasing structures.
- Weather Independence:Traditional construction can be significantly impacted by adverse weather conditions, causing delays and potential damage to materials. Prefabricated construction, being largely conducted indoors, is less susceptible to weather-related disruptions. This can lead to more predictable construction schedules, especially in regions with unpredictable climates.
Cons of Prefabricated Construction:
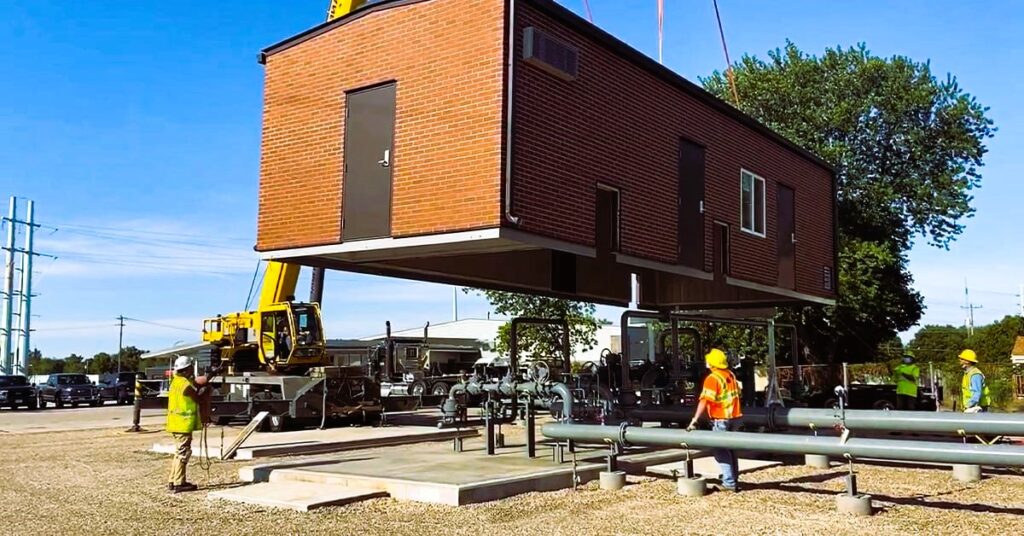
- Transportation Costs:One of the major challenges of prefabricated construction is the transportation of large and heavy components from the factory to the construction site. The costs associated with shipping oversized modules or sections can offset the savings achieved through the efficiency of the prefabrication process. A journey in the world of sustainable construction, read more in our article.
- Limited Site Customization:While prefabrication offers design flexibility in the factory, on-site customization may be limited. Once components are fabricated, major alterations become challenging, and any necessary modifications may incur additional costs. This limitation can be a drawback for projects that require significant on-site adjustments.
- Initial Investment in Facilities:Implementing prefabricated construction requires a significant initial investment in manufacturing facilities equipped for the efficient production of components. This investment may be a barrier for smaller construction firms or those not initially equipped for prefabrication.
- Perception and Aesthetic Concerns:Prefabricated construction has historically faced skepticism regarding aesthetics and overall quality. Some people associate prefab buildings with a lack of uniqueness or inferior quality. Overcoming these perceptions may require increased awareness of the advancements in prefab technology and successful examples of aesthetically pleasing prefab structures.
- Limited Size of Prefabricated Components:The size of prefabricated components is restricted by transportation constraints. Large and complex structures may require extensive on-site assembly, reducing some of the time and cost benefits associated with prefabrication.
- Dependency on Manufacturing Facilities:Prefabricated construction relies heavily on the capacity and capabilities of manufacturing facilities. Sudden increases in demand or limitations in factory production can affect the availability of prefabricated components, potentially causing delays in construction projects.
Conclusion:
Prefabricated construction presents a compelling alternative to traditional building methods, offering numerous advantages in terms of speed, efficiency, and quality control. However, like any construction approach, it comes with its own set of challenges. Builders and developers need to carefully weigh the pros and cons to determine if prefabrication aligns with the specific requirements of their projects.
For further information on prefabricated construction and industry standards, readers are encouraged to explore resources provided by Wikipedia. These platforms offer comprehensive insights into the history, methods, and considerations associated with prefabricated construction. Understanding the nuances of prefabrication is crucial for making informed decisions and navigating the evolving landscape of modern construction practices.